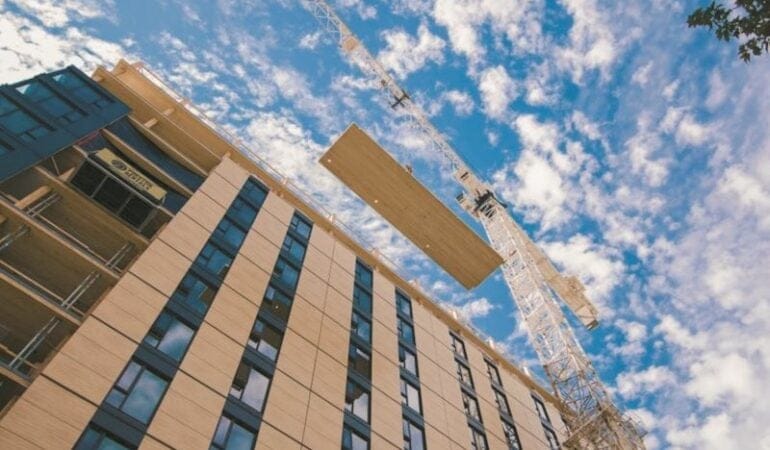
City Tech: Is Wood the Way of the Future?
When you think about innovations in development and construction, wood probably doesn’t leap to mind. It is, to put it mildly, an old-school material. But “mass-timber” construction—which involves wood panels, beams, and columns fabricated with modern manufacturing techniques and advanced digital design tools—is sprouting notable growth lately. Advocates point to its potential climate impact, among other attributes: using sustainably harvested mass timber can halve the carbon footprint of a comparable structure made of steel and concrete.
According to wood trade group WoodWorks, more than 1,500 multifamily, commercial, or institutional mass-timber projects had either been built or were in design across all 50 states as of September 2022—an increase of well over 50 percent since 2020. The Wall Street Journal, citing U.S. Forest Service data, reports that since 2014 at least 18 mass-timber manufacturing plants have opened in Canada and the United States.
The building blocks of mass-timber construction are wood slabs, columns, and beams. These are much more substantial than, say, the familiar two-by-four, thanks to special processes used to chunk together smaller pieces of wood into precisely fabricated blocks. The end result includes glue-laminated (or “glulam”) columns and beams, and cross-laminated (or CLT) slab-like panels that can run a dozen feet wide and 60 feet long. The larger panels are mostly used for floors and ceilings, but also for walls. The upshot, as the online publication Vox put it, is “wood, but like Legos.” Major mass-timber projects tend to showcase the material, resulting in buildings whose structural elements offer a warmer, more organic aesthetic than do steel and concrete.
Both the process and interest in wood’s potential have been building momentum for a while. Pioneered in Austria and used elsewhere in Europe since the 1990s, the practice has gradually found its way to other parts of the world. In an often-cited 2013 TED Talk, Vancouver architect Michael Green made a case for this new-old material: “I feel there’s a role for wood to play in cities,” he argued, emphasizing mass timber’s carbon sequestration properties—a cubic meter of wood can store a ton of carbon dioxide; building a 20-story structure of concrete would emit more than 1,200 tons of carbon, while building it with wood would sequester over 3,000 tons. Plus, mass-timber structures can withstand earthquakes and fire.
When Green gave his TED talk in 2013, the tallest mass-timber structures were nine or 10 stories high. But Green argued this new fabrication process could be successfully used in structures two or three times that height. “This is the first new way to build a skyscraper in probably 100 years, or more,” he declared, adding that the engineering wouldn’t be as hard as changing the perception of wood’s potential. Lately that perception has been getting a fresh boost thanks to a spate of eye-catching projects—including a 25-story residential and retail complex in Milwaukee and a 20-story hotel in northeastern Sweden—and proposals for even taller mass-timber buildings.
Because mass timber is prefabricated in a factory and shipped to the site, unlike concrete structures made in place, the design details must be worked out precisely in advance, requiring intense digital planning and modeling. This can ultimately make construction processes more efficient, with fewer workers and less waste. Most mass-timber projects still incorporate other materials, notes Judith Sheine, an architecture professor at the University of Oregon (UO) and director of design for the TallWood Design Institute, a collaboration between UO’s College of Design and Oregon State University’s Colleges of Forestry and Engineering that focuses on advancing mass-timber innovation. “But mass timber can replace steel and concrete in many, many applications, and it’s becoming increasingly popular,” she says. “That’s due to new availability, but also to an interest in using materials that have low embodied carbon.”
TallWood has run dozens of applied research projects and initiatives, addressing everything from code issues to supply chain challenges to building performance in an effort to help get more advanced and engineered timber into use. The institute is part of the Oregon Mass Timber Coalition, a partnership between research institutions and Oregon state agencies that was recently awarded $41.4 million from the U.S Economic Development Build Back Better Regional Challenge. That funding is meant to back “smart forestry” and other research initiatives tied to increasing the market for mass timber.
Of course, part of the newfangled material’s environmental promise depends on the back-end details, notably how and where the timber is harvested. Advocates of the sector argue that its expansion won’t cause undue pressure on forests, in part because mass-timber products can be made from “low-value” wood—smaller-diameter trees that are already being culled as part of wildfire mitigation, diseased trees, and potentially even scrap lumber.
Conservation groups and other forestry experts are proceeding a bit more cautiously. The Nature Conservancy undertook a multiyear global mass-timber impact assessment in 2018, researching the potential benefits and risks of increased demand for mass-timber products on forests, and is developing a set of global guiding principles for a “climate-smart forest economy”—best practices that will help protect biodiversity and ecosystems as the mass-timber market grows.
Often, builders and developers who specifically want to tout the use of mass-timber materials insist on sourcing that’s certified as sustainable, according to Stephen Shaler, professor of sustainable materials and technology in the University of Maine’s School of Forest Resources. “That demand is in the marketplace right now,” he says.
Beyond an interest in sustainability, there’s another reason for the proliferation of mass-timber projects: biophilia, or the human instinct to connect with nature. “Being in a wood building can just feel good,” Shaler says. That’s not just a subjective judgment; small studies have shown that wood interiors improve air quality, reduce blood pressure and heart rates, and can improve concentration and productivity.
The developers of the 25-story Milwaukee building, the Ascent, reportedly pursued the mass-timber approach largely for aesthetic reasons, and for the promotional value of its distinct look. Presumably the marketing payoff didn’t hurt: as the tallest wood skyscraper in the world, the Ascent has been a centerpiece of mass-timber press attention. But there’s another value to the public exposure: the 284-foot-high Ascent and other high-rise projects may not portend the future of all skyscrapers, but they demonstrate the possibility of safely building with mass timber at large scale. And that may help sway regulators and planners—particularly when it comes to approving the smaller-scale buildings that could be more important to proving mass timber’s real potential. “The majority of the use is likely going be in the mid-rise, six- to eight-story kind of project,” Shaler says.
The International Building Code permits wooden buildings up to 18 stories; the Ascent developers obtained a variance partly because their final design incorporated two concrete cores. As Sheine and Shaler both underscore, most mass-timber projects still incorporate at least some concrete, steel, or other materials. That’s just fine, Shaler says: mass timber should be viewed as a comparatively new option that can help improve carbon footprints, not as a full-on replacement for traditional materials. And new options are always useful—even when they’re as old-school as wood.
Rob Walker is a journalist covering design, technology, and other subjects. He is the author of The Art of Noticing. His newsletter is at robwalker.substack.com.
Image: Mass timber construction. Credit: Courtesy of ACSA.